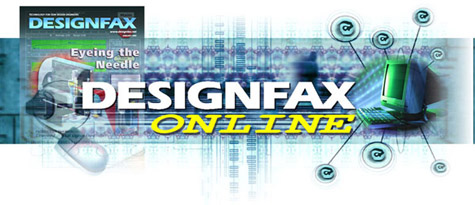
Boeing Dreamliner insider look: Fuselage production units start to roll
Vought Aircraft Industries, a program partner on the Boeing 787 Dreamliner team and one of the world's largest independent suppliers of aerostructures, is on track to deliver its first production ship set from its Charleston, SC, facility in April.
The delivery will include aft fuselage section 47, which measures 19 ft in diameter and 23 ft long, and fuselage section 48, measuring 14 ft in diameter and 15 ft long. The combined section represents 23% of the 787’s entire fuselage structure.
“Progress is well underway on the 787 program,” says Ted Perdue, vice president of Vought’s 787 Division. “It’s really exciting to see the efforts of our highly skilled workforce come together for this game-changing aircraft. The quality of the work performed by our 787 Division team in Charleston and at other locations around the world is exceptional. I am very proud of our team’s dedication and technical expertise, and I’m confident in Vought’s ability to help ‘Deliver the Dream.’”
|
|
|
|
|
Vought has completed five aft fuselage production units and one developmental unit since production began in South Carolina last year.
All of Vought’s one-piece fuselage sections, called barrels, have successfully completed nondestructive inspections (NDI) with unprecedented levels of quality. The NDI process uses high-frequency ultrasonic sound waves to scan for imperfections or voids in the skin material. Numerous tests are done to verify manufacturing processes and structural integrity of the all-composite construction.
Assembly activities are now being completed on the Vought sections before they leave South Carolina. When completed, the two sections will be joined together and transported next door to Global Aeronautica, the company’s joint venture with Alenia North America. The aft fuselage will then be loaded into a Boeing Dreamlifter and flown to Everett, WA, for final assembly. Boeing is using a fleet of converted 747-400 cargo jets to ferry components to and from partner locations in Japan, Italy, and the United States.
About half of the 787 is made of composite materials known as carbon fiber-reinforced plastic, a shift from the previous commercial airplanes constructed primarily of aluminum sheet metal and fasteners. The change in materials forced Boeing, Vought, and other suppliers to create new ways to build the super-efficient 787.
Vought is using the latest high-technology equipment to produce its barrel sections. Fabrication of the barrels is accomplished using computerized lay-down of composite tape on a large barrel-shaped mold made from interlocking mandrels. The tape consists of super strong carbon fibers pre-soaked in epoxy. The large mold rotates as the tape is applied to the surface. The uncured composite material is then placed in Vought’s autoclave for a high-temperature cure that turns the uncured composite material into a tough, reliable, and high-strength one-piece structure.
At 76 ft in length and 30 ft in diameter, Vought’s autoclave is the world’s largest by volume. It can hold more than 9 million tennis balls or 37 million ping pong balls. With a 517,000-gal capacity, the autoclave could power a car to drive around the earth 415 times.
A number of suppliers around the globe support Vought's 787 production work. The first major structural shipment from one of them arrived last week. Vought received the aft pressure bulkhead from European Aeronautic Defence & Space (EADS) business unit Military Aircraft from Augsburg, Germany. The one-piece dome, inserted between sections 47 and 48, is made using a vacuum-assisted resin transfer mold (VaRTM) process and is approximately 14 ft by 15 ft in size. It is the first composite aft pressure bulkhead ever to be used on a Boeing aircraft.
Source: Vought Aircraft Industries
© Nelson Publishing, Inc. All Rights Reserved