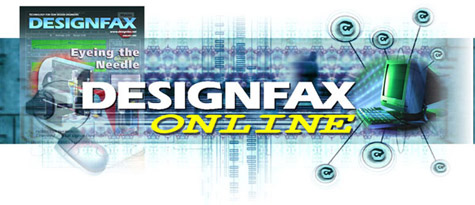
10 tips for a successful Six Sigma project
With more than 6,000 employees and operations in 50 countries, John Crane Inc. is the world's largest mechanical seal manufacturer. John Crane launched Six Sigma (a system of practices originally developed by Motorola to systematically improve processes by eliminating defects*) in 2002, and the program is credited with teaching the company how to break down the historic barriers between the geographically dispersed branch operations and the main plants. Further, the effort is credited with newfound knowledge about how to effectively collaborate, boosting productivity and the bottom line. This article outlines the perspectives about integrating Six Sigma into the operations of John Crane Latin America and shares lessons that can be applied to other globally diverse entities.
After three years of a Six Sigma initiative in Latin America, many lessons have been learned — some through trial and error and some by knowledge transfer with other John Crane facilities. As a branch operation, we recognized the importance of reaching our own acceptance of Six Sigma at all organizational levels, rather than merely implementing the management solution because it is something that the corporate office did.
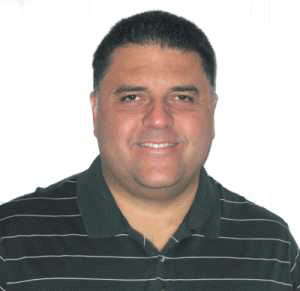
Jorge Correa, director of operations JCLA, John Crane Inc.
Acceptance is certainly something we have achieved. Today, it is impossible to conceive operating without Six Sigma because of the impact the program has had on our operations, including:
- 25% gross inventory reduction;
- 10% increase in volume of sales as well as an increase in the contribution margin;
- 14% increase in profit margin by reduction of material cost;
- 12-day reduction in cash cycle;
- 15-day reduction in cycle time;
- Improvement of on-time deliveries by 18%;
- 30% total manufacturing time reduction per piece; and
- 50% reduction of bad quality costs.
Lessons learned
Although the Six Sigma program has resulted in many projects that did not meet long-term expectations, during the course of the last three years and more than 40 projects we have been able to identify key indicators of projects that typically generate results when Six Sigma methodology is applied in an appropriate and efficient manner. This knowledge has allowed us to improve the selection of projects and to remarkably improve the probability of success. Following are the key factors that now serve as a litmus test for projects for John Crane Latin America:
1. The project must be important and strategic
The identified project must positively respond and align with a critical or vital process of the organization as well as significantly support the growth and/or profitability of the company. For example, is the project part of a strategic initiative, or is it intended to capture or retain talent? A project with these characteristics will likely have the support of key management, continuous follow-up, and the high possibility of having the necessary resources allocated to it.
2. The project must have effective leadership
Leadership for a successful project extends beyond the project leader to a champion who practices Six Sigma Leadership Principles (alignment, mobilization, acceleration, and governance). A leader must be able to communicate in a very clear way the purpose of the project to the entire team, as well as have the ability to bring out the best from each member, develop synergies, obtain objectives, and allow others to improve their own knowledge and abilities. Further, in the development of the project, the leader must promptly apply the necessary contingencies to correct deviations from the objectives and keep the team working in an enthusiastic and effective manner.
3. High-quality level training for “Belts”
With the intention of ensuring the quality of the different outputs from the project, it is crucial that Black, Green, and Yellow Belts receive high-level training according to the specific necessities in each role. This qualification must include some type of certification, probe, or test that corroborates that the trained person acquired the knowledge and is able to put it into practice. Each role requires different training levels in relation to concepts, techniques, and knowledge areas. However, the important thing is to ensure that each member of the team is provided with the opportunity to contribute a significant value.
4. “DMAIC” methodology must be followed rigorously
The leader of the team and its members must jointly make an effort to engage in all steps and technical requirements of the “DMAIC” process. (DMAIC stands for Define, Measure, Analyze, Improve, and Control). Only under special circumstances and with the Champion’s approval should any steps be skipped. Omissions, data without validation, or unproven causes typically result in ineffective solutions. To the highest extent possible, the project team should complete the key deliverables at each stage according to the established order. Further, the statistical tools and concepts should be properly utilized.
5. The time dedicated to the project must be sufficient and regular
There is a high correlation between the time of dedication and the quality of the project. Although the recommended time allotted varies depending on a variety of experts, our own experience suggests the following norms:
- Project Leaders: 75% or more of their labor day;
- Green Belts (non-project leaders): between 25% and 30% of their labor day;
- Yellow Belts: equal or greater than 10%;
- Advisors: equal or greater than 5%;
- Champions: equal or greater than 8%.
In addition to dedicated time, the time allotment should be consistent. The quality of the contribution significantly diminishes when the time is not evenly distributed (times of no work followed by times of excessive work). Further, the planning effort is very important. Whenever work meetings are going to take place or individual/sub-group assignments are going to be made, it is important to clarify what outputs or deliverables must be generated and the time-frame available to complete them.
6. The project should not last more than is necessary
Evaluation of more than 40 projects has generated sufficient data to discern a valid correlation between the project duration and its effectiveness. When a project extends more than is necessary, its effectiveness — both financial and non-financial — diminishes in an exponential way because the organization and members of the team lose interest and motivation. Experts state that the average duration of a successful project is six months; however, this benchmark is relative and the right time span really depends on the nature of the project, existence of reliable data, participation of external clients, and a host of other variables. The key lesson is that the duration of the project should be considered critical for the team and its leaders. And, when deviations occur that exceed the established limits, contingencies should be applied promptly and effectively.
7. A regular and effective review process must be followed
The review process is extremely important and must be carried out by a committee of two or three people. The key areas of focus include evaluating the validity of the data as well as the validity of the measurement system, ensuring that the statistical tools used respect the validity criteria, and verifying that the key deliverables are being generated in the right sequence and with the expected quality. The reviews must be frequent — two weeks has proven to be an effective time span — and performed by personnel of high knowledge in Six Sigma methodology. Another key element of success is that the review is conducted by the project champion. This review should focus on evaluating if the key deliverables are consistent with the reality of the organization as well as confirmation of the team’s conclusions during project development. It is recommended that the champion conducts this review on a weekly or bi-weekly basis.
8. The extended Six Sigma team must entice the company to “buy into” the project
The extended team — the Six Sigma team and its leader, the Champion, key process owners, and important collaborators — must present the project before initiating development and execution of concrete solutions in order to gain acceptance by a representative group of the organization. This high-level presentation should contain the business case, the importance or criticality of the project, the “pain” associated with the current process/system, the benefits of solving the problem, specific objectives, the root causes of the present situation, and potential solutions. In this stage, it is vital to secure the company’s commitment in the execution of action plans. It also is an excellent opportunity to receive feedback and recommendations from the organization on possible changes and project adjustments.
9. The organization must have an attractive reward system for the successful projects
As mentioned in the very first factor, the project must solve a critical and/or strategic problem of the organization. Consequently, it is therefore reasonable that the organization shares at least part of the generated benefits. The reward must have two characteristics:
- Provided to the entire Six Sigma Team. All members, in their different roles, must receive some type of reward proportional to their contribution in the project. It is important to validate with the leader and champion the actual contribution of the team members during the entire period of the project development.
- It must be significant. The reward must be important and highly valued by the members of the team. Although there is a wide variety of opinions on what is appropriate — ranging from cash to temporary benefits, trips, promotions, meals, public recognition, and more — the most important factor is ensuring that the team members feel that they are being compensated in a fair and prompt way for their contribution.
10. The project must include an effective and simple procedure to ensure its continuity on the daily work of the organization
Once the Six Sigma team has practiced and demonstrated the improved process in repeated opportunities, it is time to pass it on to the process owners who will be responsible for its continuing delivery. It is vital that the Six Sigma team develops a process delivery plan that includes process flow charts, control check points, specification limits, responsibilities of the process owners, training schedules, contingency plans for deviations, manuals, and more. Further, the Six Sigma team must continue to observe the improved process for a reasonable time period to ensure that the organization has normalized the improvement.
Putting the elements into practice
As one would imagine, the aforementioned factors do not work in an isolated manner. Rather, they are intimately related, and any weakness observed in the application of one will have remarkable repercussions on the others. In contrast, by incorporating these elements into your process improvement projects — even if they aren’t through a Six Sigma program — is likely to generate successful results.
Jorge Correa is an industrial engineer with 21 years of experience in international operations. He has a Master’s Degree in Industrial Management and a post-graduate program in Advanced Management. He also is Black Belt certified and APICS certified and has developed several improvement programs based on the Theory of Constraints and Lean Manufacturing. Correa has worked in all areas of manufacturing and distribution including production and inventory control, production, engineering process, quality assurance, inventory management, and procurement. During the last seven years, he has occupied the position of operations director of John Crane Latin America. Since January 2004, he has served as the Six Sigma program director, responsible for managing the initiative for the region. Further, he was part of the team responsible for preparing the John Crane Latin America Strategic Plan. Today, he has an active role measuring its effectiveness and progress.
*Wikipedia short definition.
Want more information? Click below.
John Crane
© Nelson Publishing, Inc. All Rights Reserved