March 27, 2012 | Volume 08 Issue 12 |
|
 | New ‘pin and keeper' quick-assembly sign fastening system The Micro Plastics sign fastener is designed for rapid assembly and disassembly of a sign or other panel to its support structure. The reusable fastener was designed to fit a hole diameter of 5/16 in. to 3/8 in. (8 mm to 9.5 mm) and can be used to fasten two pieces together with total panel thickness from 1 in. to 1.64 in. (25.4 mm to 41.6 mm). Simply squeeze the keeper together and slide onto the pin, then release the keeper. Molded from impact-resistant and UV-stabilized nylon 6/6, the sign fastener is designed to withstand the elements in outdoor applications.
Click here for more information. |
New process clads gold contacts with a laser Electroplating is the conventional method used to plate metal switches, but scientists in Germany have developed a new and novel laser-based method that involves laser-cladding gold contact spots instead of applying the gold in a thin layer on the whole surface. This new technique is fast and offers the potential to cut up to 90% of the amount of gold used.
Read the full article. |
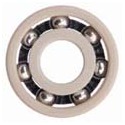 | Mike Likes: Lubrication-free plastic ball bearings for extreme applications Able to withstand temps to 302°F, xiros ball bearings from igus have opened new fields of application for plastic bearing technology. The inner and outer races are made from high-performance iglide polymer materials, while the corrosion-resistant balls are made from stainless steel. Glass balls are also available for maximum corrosion resistance. Lightweight and maintenance free, these bearings are available from stock, and an FDA-compliant option is available. Calculate how long xiros ball bearings will last in your application and learn all about the xiros line, including slewing ring bearings and self-aligning flange bearings, by clicking here. |
| Videos+: Technologies and inspiration in action |
Autonomous robot arm is an attention grabber DARPA's Autonomous Robotic Manipulation (ARM) program is developing software to perform human-level tasks quickly with minimal direction. This video shows the ARM robot performing 18 grasping and manipulation tasks using vision, force, and tactile sensing with full autonomy – no active human control. The DARPA-supplied robot was built using commercial components that include an arm, hand, neck, and head sensors. Rigorous testing in November 2011 achieved 93% success in grasping modeled and unmodeled objects. The ARM program has entered its second phase, where the focus turns to complex bimanual manipulation scenarios.
View the video. |
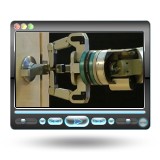 |
|
|