July 16, 2013 | Volume 09 Issue 27 |
|
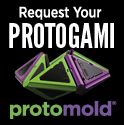 | What the heck is a hexa-kaleidocycle? It's Protogami, a 3-dimensional folding object that showcases the interaction of materials and surface finishes -- an interactive design aid from Proto Labs. Broaden your knowledge of surface finishes, materials and design techniques by requesting one today. You'll learn, you'll be endlessly amused, and you just might be inspired to come up with the next big thing.
To get your no cost Protogami design aid, click here. |
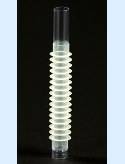 | Rogan's Liquid Silicone Rubber Molding Capabilities In business since 1934, Rogan Corporation is a leader in the injection molding industry, producing thermoplastic and LSR (Liquid Silicone Rubber) components and assemblies. Manufacturing LSR components is a rapidly growing segment of the business. Rogan is one of a few select manufacturers that offer Bondable LSR overmolding. This process involves the injection molding of a bondable-grade silicone directly onto plastic or metal parts, creating a single integrated component. LSR's heat, chemical, shock, and vibration resistance along with its sound-dampening characteristics have made it an ideal fit for integral seals and gaskets, waterproofing complex geometries and electronic interconnects, integral membranes, diaphragms, valves, and switch covers. (Photo showcases .008" thick fins bonded to a plastic tube.)
CLICK HERE to learn more about Rogan's Liquid Silicone Rubber Molding capabilities and Class 100,000 Clean Room.
CLICK HERE for an overview of Rogan's comprehensive injection molding capabilities. |
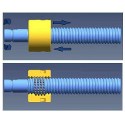 | Engineer's Toolbox: Selecting and sizing ball screw drives Ball screw drives typically provide mechanical efficiency of greater than 90 percent, so their higher initial cost is often offset by reduced power requirements. Jeff Johnson, product engineer at Thomson Industries, gives an in-depth description of ball screw technology, important ball screw specifications and applications, and a lengthy and technical selection and sizing example.
Read the full article. |
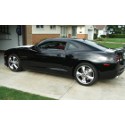 | Readers tell us: Why I love my car What engineer doesn't like to talk about cars? Now it's your turn to tell us why you love yours -- and the engineering behind it. Email a paragraph or two and maybe even a pic, and we'll post your story in an upcoming issue of Designfax. John from Lincoln Electric never forgot his first car, a used blue Camaro he got when he was 16 ...
Read the full article. |
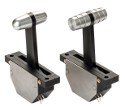 | Product Spotlight: Precise T-bar controllers have a multitude of applications The SN series precision T-Bar fader controller from APEM features contactless Hall-effect technology that provides reliable, noise-free operation and absolute positioning, which makes the controllers ideal for music studio equipment, video and image editing systems, lighting panel equipment, and sound and broadcast panels. Magnetic shielding protects the SN series from outside interference to ensure the controllers are not affected by other devices, and precision ball race bearings and PTFE guides provide a consistent smooth feel. Plus, the "barrel" and "bullet" aluminum handle options look really cool.
Click here to learn more. |
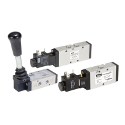 | Product Spotlight: Viking pneumatic valves go Xtreme Parker Hannifin has expanded its line of Viking Xtreme Valve Series solenoid and remote pilot valves with a 3-way, 2-position option to provide a wider range of applications from general industrial to rugged environments. The Xtreme Series has passed 5-g shock in vibration tests and was specifically designed for harsh applications in transportation, lumber, oil and gas industries, mining, and more. It features stainless steel armatures and a remote air-piloted valve, and it works in temperatures ranging -40 deg F to 140 deg F and pressures ranging from vacuum to 232 PSIG.
Click here to learn more. |
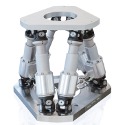 | Product Spotlight: New high-load hexapod production and test facility PI (Physik Instrumente) recently added a new building with more production floors, metrology labs, and R&D office space to its factory in Karlsruhe, Germany. Close to 4,500 sq ft are dedicated for the manufacture and test of heavy-duty 6-axis motion systems capable of moving loads up to 5 tons with sub-micrometer precision. A giant lift and rotation platform is used to spin the 6-axis positioner with its load by 360 degrees to verify performance under the exact mounting conditions of the customer's site. Neat fact: Fifty of PI's hexapods align reflectors in the ALMA (Atacama Large Millimeter Array) observatory, the world's most advanced telescope located in Chile.
Click here to learn more about PI's hexapods. |
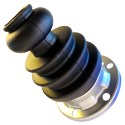 | Product Spotlight: First blow-moldable thermoplastic vulcanizate (TPV) introduced A newly developed extrusion blow moldable Viprene thermoplastic vulcanite (TPV) grade 1748 is now available from Alliance Polymers and Services (APS). The material can be press blow molded, suction blow molded, or 3D sequential coextruded, which offers new opportunities for designers and manufacturers to economically mold automotive, aircraft, and other vehicle parts for applications including hollow boots, bellows, and ducts. This material is a comparable alternative to competitive, higher-priced TPVs and can be substituted for more costly parts made of silicone or ethylene-acrylic rubber.
Click here to go to the APS site. |
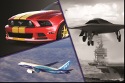 | Events: 2013 Boeing, Northrop Grumman Global Product Data Interoperability Summit attendee registration closes July 31 The attendee registration deadline for the Boeing Company, Northrop Grumman Corporation, and Elysium Inc. Global Product Data Interoperability Summit (GPDIS) is July 31. This year's theme for the event, to be held September 9-12 at the Sheraton Wild Horse Pass Resort in Chandler, AZ, is "Enabling Productivity with Common Data Streams." The GPDIS functions as a communications hub for industry professionals to exchange ideas, solutions, and methods for improving product data quality and interoperability, with the goal of driving common standards adoption in global aerospace, automotive, and other industries.
Click here to learn more. |
| Videos+: Technologies and inspiration in action | Save time and money on large-scale, high-value parts and prototypes with Sciaky's Direct Manufacturing Sciaky's Direct Manufacturing (DM) is the only large-scale, fully programmable means of achieving near-net shape parts via additive manufacturing made of titanium, tantalum, inconel, stainless steel, and other high-value metals. Starting with a 3D model from a CAD program, Sciaky's fully articulated, moving electron beam welding gun deposits metal, layer by layer, until the part is complete and ready for finish machining. Deposition rates typically range from 7 to 20 lb/hr, depending upon part geometry and the material selected. Sciaky's DM has a standard build envelope of 19 x 4 x 4 ft, allowing manufacturers to produce very large parts and structures with virtually no waste. This is cool to see in action.
View the video. |
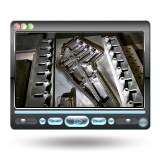 |
|
|