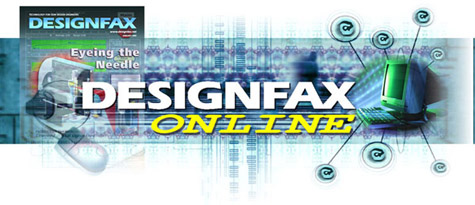
It’s revenge of the NURBS for mega-yacht design

The Rhinoceros modeling software, now used throughout the marine industry, allows Delta designers to easily generate streamlined nautical features ready for both fine rendering and accurate CNC manufacture. RhinoMarine, an additional plug-in provided by Proteus, aids in generating hull shapes.
“We’re in the top tier of yacht builders in the world,” says Delta Marine Industries senior designer John Cantu. “We’re known for very smooth, well-finished exteriors.” While Delta’s award-winning mega-yachts include interior décors that rival those of the finest world-class hotels, it is their sculptural exteriors that give Delta yachts their distinctive elegance.
The style of Delta’s fully custom yachts combines classic sophistication with the modern curves that could only come from today’s most advanced design and production techniques. Cantu and his associate, senior designer Joe Petrich, attribute the firm’s success to a close collaboration with clients, as well as the intelligent use of 3D design technology. 3D tools not only shape the distinctive look of Delta’s yachts, but have in many ways shaped the evolution of the firm.
Delta’s products are born from its shipyard on the Duwamish River on the south end of Seattle, where Delta began in the 1960s as a builder of fishing boats. Its output in this period — over 800 units — has earned the company a worldwide reputation for durable construction with hulls designed to brave the harsh waters of Alaska and the Bering Sea.
“Around 1985, the fishing industry declined,” recalls Petrich. The firm segued from boats for industry to boats for pleasure. “We started building a 70-ft motor yacht based on a crab-boat hull. That model was very successful. From there, we’ve worked our way up. In 2006, we delivered the largest yacht built in the U.S. in over 75 years, at 240 ft.”
Only a few years after Delta’s foray into the world of high-end yachts, another Seattle pioneer was making changes to his own company, which would ultimately prove influential to Delta’s design process. Petrich heard from his local AutoCAD vendor, Robert McNeel. McNeel asked Petrich to help test a new three-dimensional surface modeler called AccuModel. McNeel & Associates soon changed the name of the software to what it is known now by industrial designers around the world: Rhinoceros.
“When the first betas of Rhino came out, I took the test versions and started working with them at Delta to develop our parts,” says Petrich. “We found we could use the 3D process. It went on from there.”
In the ensuing years, Delta rose to become the top trendsetter of the maritime industry, and Rhinoceros, now on version 4, surged in popularity among designers with modeling needs that went beyond rectilinear forms. Still a privately held company, McNeel & Associates has kept the cost of its software low, its operation and features understandable, and its architecture open to third-party programmers.
“McNeel really concentrated on getting the creation of curvilinear surfaces perfected, which is useful for a lot of our complex designs. It’s more organic than many other software packages that aim solely at mechanical design,” says Petrich.

Super pieces for mega-yachts — Delta’s curvaceous superstructure components are modeled in Rhinoceros. Once completed, the 3D data guides production. 88-foot-long CNC machines at Janicki Industries in upstate Washington automatically carve out the casts for Delta’s yacht parts. 1) Flybridge, 2) Foredeck mold, 3) Pilot house, 4) Louvers.
Both Petrich and Cantu now use Rhino intensively at Delta, along with a dozen other team members who use the application to varying degrees. “The commands are very comparable to AutoCAD, so anyone can pick it up very easily. Even non-designers can navigate it, open a model, and get the information they’re looking for,” explains Cantu.
After general design sketches are created for the client, Delta designers use Rhinoceros to develop the curvatures of the hull form, while at the same time using AutoCAD to lay out floor plans of the deck and cabins according to the clients’ preferences.
The challenge, says Cantu, is to ensure the interior layout and exterior curves come together accurately. “Rhino is the perfect program to be at the center of a 3D process, because it imports and exports basically all other formats,” Cantu says. The Rhino model becomes a central hub to organize all the disparate aspects of a massive yacht project.
“The time it takes us to design a hull form and all its associated parts has been reduced dramatically,” says Petrich. “A hull used to be developed in line drawings by hand. It took weeks and weeks just to get the basic lines for the shape of the hull. And now with 3D tools, we can make three to four iterations of different hull shapes a day.”
The designers also take advantage of a third-party plug-in developed by Proteus Engineering called RhinoMarine, which “allows us to do hydrostatics and stability calculations inside Rhino, which we’ve found very useful,” says Petrich. “We can predict the way the yacht will perform in the water much easier, given its horsepower, weight distribution, and hull shape.” A typical Delta yacht can reach speeds approaching 20 knots and carry enough fuel to cross an ocean.
Delta’s engineering professionals continue calculations on the 3D hull shape using ANSYS software, a specialty program for finite element analysis. “ANSYS allows us to develop the 3D structure efficiently, so we don’t over-engineer something based on regular calculations. “We can fine tune the craft,” says Petrich. “Once the engineers are happy with what they have, then we start cutting up the Rhino model into buildable sections of hull and superstructure.”
Production of ships has also been modernized with the advent of 3D data. The Rhinoceros modeler is based on NURBS — the name for curved surfaces described by mathematic equations. These precise descriptions give designers the ability to build any conceivable 3D form with the high accuracy needed to guide computerized factory equipment.

Delta imports its 3D models into ANSYS software for finite element analysis, which allows engineers to optimize weight distribution and predict performance characteristics.
“We send the parts modeled in Rhino off to Janicki Industries, an hour and half north of Seattle. The company owns several very large five-axis CNC machines with envelopes 88 ft long, 19 ft wide, with 8 ft of Z-movement,” says Petrich. “They build our molds for fiberglass pieces, which we truck to Seattle and use to fabricate the superstructure parts in our yard.”
The molds are constructed out of syntactic tooling foam, supported by a plywood base. Shipbuilders apply layers of fiberglass, carbon fiber, polyester, vinylester, or epoxy resins to the mold surfaces. “We now use a resin infusion technique to build parts,” explains Petrich. “You put down all your layers and cover it in a bag, draw a vacuum through the bag, and feed resin through the vacuum. The resin permeates the parts and compacts the whole package so you get a stronger fiberglass structure.”
Delta specializes in composite construction, but in recent years the firm has expanded its options for clients to include steel or aluminum structures, which employ a similar 3D design and production process.
For Cantu, the effects of technology on yachts go beyond the internal efforts. Yachts themselves have changed. “What you see is a more sculpted look, more of emphasis on shape — more style,” he says. “3D models allow customers to get very specific in terms of the forms they want. A model can communicate so much more than a sketch of a hull profile. Today the marine industry has all the 3D capabilities of the auto industry and it is starting to show in the styling.”
Delta’s clients are involved at every stage of design development, and the firm prides itself in satisfying customers in every aspect of the finished project. Cantu produces the photorealistic renderings of the Rhinoceros model for client review. He uses Maxwell Render by Next Limit Technologies, which can sometimes run microprocessors as long as overnight but produces brilliant, super-high-resolution depictions.
“In the last year, Rhino users have been fortunate enough to get their hands on rendering software formerly reserved for Hollywood film studios,” he says. “With rendering software like Brazil R/S beta and Maxwell Render, there is no reason we should not be producing renderings with the same professional quality.”
“The 3D model has really helped to streamline the process of design approval,” Cantu adds. “We can rotate the Rhino model on a big screen in a conference room during client discussions, or dress the model up as a full rendering.”
DESIGNER'S TOOLBOX Delta Marine Industries, Seattle, WA
|
As world-class designers of yachts, Cantu and Petrich prefer digital tools that have a straightforward simplicity and effectiveness, rather than systems laden with complex and hard-to-use features.
“Rhinoceros isn’t weighed down with a lot of features we don’t use, but then again, with plug-ins, we can have all the extra features according to our specialty,” says Petrich. “McNeel & Associates leaves the architecture open enough that the modeler fits together with some really great third-party plug-ins like RhinoMarine and a lot of others. The rendering programs, too, work with Rhino especially. John can render some great stuff.”
“In Rhinoceros, I can always make the shape I want very quickly,” says Cantu. “And once I’m there, the rest is a very good process.” Cantu relates that other designers are often surprised that a modeler that costs only a tenth of the price of other styling packages can have a full spectrum of capabilities.
As such, use of the Rhinoceros surface modeler has spread all over the marine industry, making it even easier for Delta Marine to do business. “Many of our contractors use Rhino, like Belina in Tacoma, the company that works with us on our interiors. A lot of people in the marine industry use Rhino now, whether power or sail, or commercial or pleasure,” says Petrich.
Want more information? Click below.
McNeel & Associates — Rhinoceros
Want more information? Click below.
Proteus — RhinoMarine
Want more information? Click below.
AutoCAD
Want more information? Click below.
ANSYS
Want more information? Click below.
Next Limit Technologies — Maxwell Render
Want more information? Click below.
Delta Marine Industries
© Nelson Publishing, Inc. All Rights Reserved