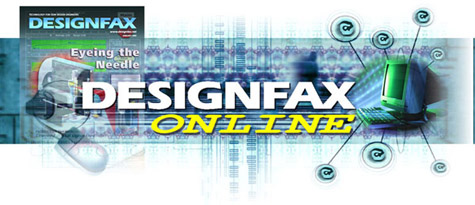
Pro/E vs. SolidWorks — a working comparison
Product Development Technologies (PDT), a full-service, award-winning product development firm headquartered in Lake Zurich, IL, is known as one of the largest users of Pro/ENGINEER (a 3D CAD parametric feature solid modeling software) in the world of product consulting. With 50 licenses, 80+ users, and more than a million hours of Pro/E experience collectively among its team, the company has truly earned that reputation. In recent years, however, PDT has had more clients requesting databases created by Pro/E’s competitor, SolidWorks, as their end deliverable, and so the company has grown its SolidWorks expertise to meet that need.
With a great deal of confusion in the market about the relative strengths of each of these CAD software packages, three PDT mechanical engineers were willing to sit down and share their experiences and compare the two side by side. Bjorn is a Pro/E expert from PDT’s Chicago office, Steve a SolidWorks master from Lake Zurich, and Stanislav is the company’s switch-hitter for both teams, working from PDT Ukraine.
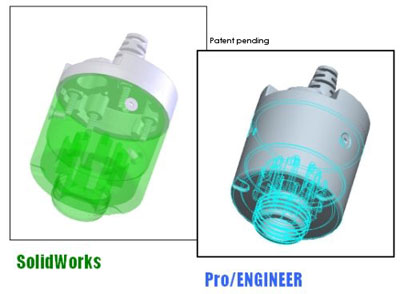
Bjorn: In the past we always used SolidWorks sort of begrudgingly. We learned it on the fly … we’d start the work in Pro/E, then our counterparts in Ukraine would convert it into SolidWorks. The way it progressed through PDT was great, though, because it made for fantastic training for our Ukraine team, who are now top-notch SolidWorks experts. Now, if a client uses SolidWorks, we’ll start there rather than in Pro/E because we have team members who are experts both in the U.S. and abroad.
Stanislav: That’s right. It was a crash course in both of the softwares as well as effectively and efficiently communicating with overseas team members. In my opinion, SolidWorks is intuitive and, dare I say, simple. Pro/E is more advanced with a huge amount of optional licenses and opportunities — strangely, though, there’s still no polygon feature in Wildfire 2 …
You don’t have to read a manual to figure SolidWorks out. On the other hand, you wouldn’t learn Pro without a manual or a good teacher.
Bjorn: The biggest downfall of SolidWorks in my opinion is the inability to share geometries and features across parts. Pro has a master part so all your outside surfaces, location of keys, features, sketches, datum points, axis — anything — can be shared among all of your (potentially thousands of) parts.
For a candy bar cell phone, for example, there’s a battery door that comes off. When the battery door is put on there, it needs to be smooth and integrated and exactly matching up with the back surface of that cell phone. If you can create all that geometry in one location and have it shared into the housing and the battery door, you can guarantee that the housing matches the battery door and that they’re all based off of one thing. In SolidWorks, you can do that, but it’s almost rudimentary compared to the way Pro/E handles it.
Steve: SolidWorks will carry surfaces, planes, solid geometry, and axis. It won’t let you share curves, but the work around is instead of a curve, you extrude a millimeter surface.
Bjorn: That’s really clunky. I think for serious projects, that’s a big negative.
Steve: I’ll give you that the whole concept of a master part is not as developed in SolidWorks as it is in Pro/E. This is definitely one area in which Pro/E is superior. However, it is easy to get used to defining features and sketches in assemblies in SolidWorks. So external geometry and surfaces can be defined in a master model and then split off, assembled in a master assembly, and have features added to them in the context of the assembly.
Stanislav: Pro/E has more sweep options and surfacing is much easier.
Steve: You’re right … there are issues with lofts and sweeps, but SolidWorks TRIES to make things work. In Pro/E, you just get errors. I like that at least an attempt is made even if you do end up with some funky surfaces at first.
Stanislav: Pro/E is complicated but it allows you to do any geometry you want in it; you just have to know how to do it. I actually think SolidWorks is strong in solid features and surfaces but weak in drafts and rounds.
Bjorn: Pro/E’s surfacing is better because there are some things you can’t do in SolidWorks. In SolidWorks, there tend to be issues with lofts and sweeps if they aren’t smooth. If they have edges that don’t match up to what you’re lofting to, you get those funky surfaces. I think it’s worth noting that a number of our industrial designers work in SolidWorks occasionally. There’s a stigma that goes along with Pro/E that the learning curve is steep, but Pro/E changed their user interface drastically in the last six years. They went away from the menu picks and tried to pull a lot out of the menus out into icons. I think it’s more intuitive now.
Steve: Engineers are typically trained to be very structured in the way they think, so you find that many engineers prefer the logical structure and process involved with developing and defining features in Pro/E. After all, Pro/E stands for Pro Engineer. It was designed, developed, and tested by engineers, so it’s going to have a logical feel to it.
I have found that the more creative half of our industry, the industrial design sector, prefers to use SolidWorks for the interface. It basically comes back to preference: bland with a pinch more speed or easy to use but a tiny touch slower.
Stanislav: SolidWorks doesn’t change its interface from version to version, it just adds features — you’re not relearning each revision.
Steve: It also leverages the average person’s knowledge of Windows and uses a lot of familiar interfaces. For example, the way you save files is the same way you’d save them in Microsoft Office.
Bjorn: True … but I do love Pro/E’s working directory. Once you grow accustomed to using it, it’s a fantastic file management tool.
Steve: If you’re working with any mechanism where you need to see motion, SolidWorks is the only option — it handles kinematics beautifully, measuring velocities, motion, acceleration. It has special mates for gears …
Bjorn: You’re right. I’ve taken data from Pro/E and put it into SolidWorks so I could see the mechanism in action. If you have two parts moving, Pro/E is fine, but it you have, say, a four-part linkage, forget it. The other option is just build a physical prototype.
Stanislav: I would like to touch on the assembly aspects of both programs. I believe, and get almost unanimous agreement, that SolidWorks is superior when it comes to mating parts or assemblies.
Steve: Yes! Recently I used an advanced mating feature in SolidWorks that allows you to set angular or linear limits. Technically, the model was fully constrained, but motion was allowed within the limits defined by the mate. I’m pretty sure this can be done in Pro/E, but it may be much more involved.
Stanislav: What’s great about having expertise in both softwares is [that] if we get an .iges or .stp file occasionally SolidWorks is better at importing it, sometimes not. It’s great to have both because you don’t necessarily know which will be better. This is especially an issue when it comes to data from laser scans or during a reverse-engineering exercise.
Bjorn: Of course, in the end, the determining factor for us on what software to use at PDT is solely based upon what the client needs. Whether they need a SolidWorks or Pro/E model, we can do that.
Special thanks for this article goes to Product Development Technologies, Inc., Steve Jones, Bjorn Gunderson, Stanislav Dmitriyev, and Tanya Sillitti. www.pdt.com.
See the latest that SolidWorks has to offer at www.solidworks.com
See the latest that Pro/ENGINEER from PTC has to offer at www.ptc.com
© Nelson Publishing, Inc. All Rights Reserved